In this blog post Kidambi Kannan, Technical Manager from AutoForm Engineering USA, discusses the best evaluation methods towards representing material behavior for simulation. From understanding coils to examining yield surface models, Kannan provides an overview of the underlying material theory behind formability analysis. You are now reading Part 1 of a 2 part series!
Indeed! And it is interesting to understand how, when it comes to designing sheet metal products and the stamping processes that produce them. Interesting turns to important, very much so, in how we characterize and represent different aspects of material behavior in simulation.
Sheet metal properties relevant to cold stamping may be broadly classified into “physical” and “mechanical” properties, and limit conditions that help with prediction of failure. Physical properties include elastic “constants,” the Young’s Modulus and Poisson’s Ratio, and the density of the material. Mechanical properties represent the plastic deformation response (“strain”) of the material as the applied load (“stress”) increases.
Sheet metal for stamping applications is most commonly characterized through tensile testing. Typical tensile specimens, and stress-strain outcomes are shown below.
Stress-Strain curve captured in a tensile test
Elastic and plastic characteristics are marked on the stress-strain curve outcome of the tensile test. Given the repeated rolling of the sheet metal during the production of the desired final gage, it is easy to understand that sheet metal develops a “rolling bias,” leading to properties that are different when tested in different directions.
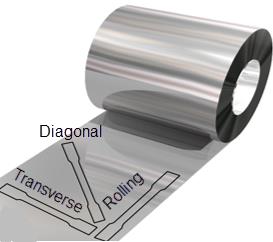
The magnitude of these differences depends on the material grade, and the processing the coil undergoes en-route the final gage. It is therefore important to characterize material in multiple directions; this is typically done along, perpendicular to (transverse), and diagonal to, the rolling direction of the coil. “R-values”, representing the anisotropy of the material, is calculated from these tests.
The tensile test represents a simple, uniaxial (one dimensional) load application; its outcome, the stress-strain curve, therefore represents no more than uniaxial plastic deformation, or hardening behavior. During the stamping of complex panels, sheet metal experiences multi-directional loads, and therefore multi-axial deformation. “Yield” surfaces are multi-directional generalizations of yielding / hardening behavior; these are models that are fine-tuned and validated through physical testing.
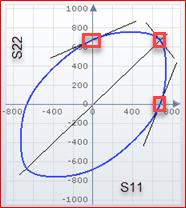
And it is the yield surface that also carries the effect of sheet metal anisotropy, as influencing the slope of the yield curve at the marked intersections ( ), and thereby the also the shape of the curve between the these intersections.
Although cold stamping production presses operate at a high stroke rate, the final stamped shape is not an instantaneous outcome: as sheet metal is stretched between upper and lower die shapes, it develops deformation (strain) progressively; stresses build in the material progressively; magnitude of stresses is a function of inherent plastic behavior of a material. If this plastic behavior is insufficiently characterized or inaccurately represented in simulation, it clear that the stress response to a deformation state will be inaccurate. This has strong consequences all around:
- If the current stresses are calculated inaccurately, the progression of deformation strains will clearly be inaccurate; these inaccuracies add up through the entire stamping process to produce bad deformation and stress outcomes,
- Bad deformation outcomes lead to incorrect assessment of panel failure or safety, as well as all of the other quality metrics,
- Springback is the consequence of relaxation of stresses; this is strongly influenced by how much stresses accumulate on the panel, and how these are distributed over the panel. Needless to say, springback predictions based on inaccurate / incorrect stresses are worthless.
See below for differences in deformation and springback outcome for different choices of commonly available yield surface models.
Formability outcomes
Springback outcomes
Which of these outcomes is trustworthy? In other words, how can we ensure simulation outcomes are reliable? Let’s focus here simply on material representation in simulation, assuming die and process conditions are faithfully represented.
Physical constants seem to be just that, constant, and so easy to deal with, for a given class of materials. This is not quite the case for the Young’s Modulus. In terms of Continuum Damage Mechanics, and based on experimental evidence, Young`s Modulus is also clearly influenced by the magnitude and history of deformation; but we will come back to this in detail later.
Today, three-directional tensile testing is quite commonplace; these tests produce stress-strain curves, and the “r-values” that represent material anisotropy. It is important that the raw stress-strain data generated along the rolling direction be imported as is for the most faithful representation, in simulation, of the material’s hardening behavior, as against imposing theoretical models such as Ludwik, Swift, etc. on these raw data.
How do we represent the yield surface of the material? This cannot be measured, except at special points on the surface. A handful of good models are available for application to common material classes used in automotive stampings. Recent and sophisticated models demand more data points from testing, in addition to tensile, and build a closer representation of the yield surface. The more the data demanded by a model, the closer its representation can be expected to be to a material’s actual yield behavior. The downside to such models is that testing for all the necessary data points is expensive and rarely available.
So let’s start from the other end: what data are commonly available, and inexpensive to generate? And which of the available models is best suited to take advantage of these?
Let’s consider stress-strain, anisotropy and related information from three-directional tensile testing. Three models commonly available in commercial stamping simulation software that build yield surface representations based on tensile data: Hill, BBC and Vegter.
Different shapes of Yield Surfaces for three different models
Which of these is most representative of a material’s behavior? Each of these models builds a unique shape of the yield surface, which is then calibrated to specific dimensions using the data from tensile tests. Of these, Hill uses just four data points generated from tensile test, BBC uses six, and Vegter 2017 uses ten. BBC actually requires data from bulge testing in addition to tensile, and Vegter requires data further from compression, shear and plane strain testing. Data from such advanced testing is rarely available; this challenge is overcome in common implementations of BBC and Vegter (Vegter 2017) where the missing data points are internally calculated just from those available from tensile tests.
Best representations are of course those built from test data for all required data points; limited sets of material cards are indeed available from some material suppliers based on such extensive testing. More often, however, we are left to build a yield surface based on more commonly available tensile data; it is reasonable to expect a better quality representation from models utilizing more test data to calibrate yield surface shape and dimensions.
An important take away thus far is to build material representation of hardening and yield surface based at least on three-directional tensile data, and to take advantage of models that rely on more data points from these tests. This is crucial for all aspects of simulation outcome: deformation (strains), stresses, history, and for springback.
Is this sufficient however to ensure reliable and accurate springback, towards compensation? Particularly for the newer grades of advanced high strength steels, and aluminum alloys, both of which are increasingly applied towards meeting light weighting and safety targets?
Let’s find out from Part 2 of this discussion …
I would like to acknowledge all those various AutoForm authors for the images used in the above.
New readers, don’t forget to sign up to our blog. Zero marketing emails sent to you. Just one monthly top posts blog update.