Two Roller Passes or Three Determined by New AutoForm User
The results of the hemming process have a significant impact on appearance and assembly of the parts. All too often, OEMs spend a lot of time redesigning the process of the outer and inner panel due to issues arising from hemmed assemblies. Thus, the ability to simulate and evaluate hemmed assemblies is critical, especially when manufacturers could bypass the process of having to redesign. In this blog post we demonstrate that a design engineer for single parts without previous hemming experience can determine practical hemming processes with the software.
Figure 1: Die hemming left, roll hemming right
Since its introduction, finite element analysis has given us a new path to work sheet metal forming and the ability to predict the results of the assembly. Different companies have developed software capable of predicting the results of sheet metal forming. Learning new software is very time consuming however, and can present a steep learning curve. AutoForm’s QuickHemming approach allows the use of an outer sheet geometry and a defined inner for hemming simulations and is able to quickly generate hemming tools or modify the process. This can be done without need to use other software. AutoForm has the capability to setup the highly productive process of die hemming, tabletop hemming and the more flexible roll hemming. Both setups require hemmed or flanged outer designs and the appropriate representation of the inner part in the software. Users will have either to define or to import the hemming bed and hemming tools. The steels for tool hemming are generated by user defined settings like number of passes required. For roll hemming processes, AutoForm has generic and modifiable roller templates (Figure 2). Along the tool path, users can place in-points and out-points which enables engineers to define attack angle and tool position. The setup of the process is simple and different angles driven by the part geometry are accounted for automatically.
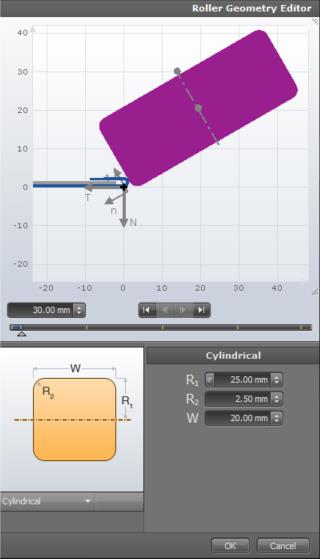
Now to the question of three roller passes vs. two for hemming. Using three roller passes potentially creates more dimensionally accuracy for correct assemblies. Yet it is justifiable to sacrifice tooling cost and cycle time for a lower volume of panels. However, an optimal volume of panels generated in the selected process variation has to be approached differently, executed in just two passes, at 45 and 0 degrees. An experienced process engineer could determine the number of passes required for specific geometries in practice from or they are defined in standards. However, engineers with virtually no background in FE-slimulation can let AutoForm indicate critical areas and obstacles in their single part designs, as the software has given the ability to identify the shortcomings of using proposed hemming procedures..
In order to best compare, two simulation files were setup for experimentation. One used two roller passes and the other three roller passes respectively. All roller geometries were identical, as the geometries didn’t have much of a contribution to the interested results variable. The user was able to experiment with different roller paths to come up with the solution. Besides formability, the results, roll-in and hem deviation, on both panel turns out to be relatively similar (Figure 3). Using AutoForm, the user was able to prove that a two-pass hemming process was effective for the given geometry.
Figure 3: Hemming results – two rollers (left), three rollers (right)
Ultimately, as we may express “the die is cast” – it is extremely difficult and time consuming to redesign the draw and trim process for single parts. The right approach is to maintain the mentality that one must fix potential issues before the tooling has been created, and feasibility analysis should be implemented as early as possible in the product development cycle. AutoForm ensures a steep learning curve and saves time consumed in redesign, which is crucial in our fast-paced environment. Even better, AutoForm gives the users the ability to evaluate and systematically improve the hemming and tools regardless of more detailed experience in hemming simulation and draw meaningful conclusions for the design of their single parts.
Don’t forget; if you haven’t already please sign up to our blog. We’ll send out just one email per month on our latest top blog posts for you.