Today, I would like to talk about the high-strength steel part compensation analysis of our long-time customer, IJS (Ilji Tech Tooling Factory). IJS manufactures tools for various parts. Recently, they’ve been experiencing difficulties with springback compensation in the production of tools for high-strength steel parts. In fact, when it comes to high-strength steel part compensation, I believe that all companies struggle to manage springback.
Since 2016, IJS has tried to reduce the gap between the simulation analysis and the tool shop results. Their tool designers are now trained to apply the tool shop conditions to the simulation. More recently, they have dedicated their efforts to strengthening the feasibility simulation and optimizing virtual iterations using simulation. IJS states they’ve been using AutoForm to derive fast and accurate results — which has enabled them to enhance the feasibility simulation. In addition, they are trying to ensure that the simulation conditions are matched by the real tooling in the tool shop.
In the past, IJS’s process was as follows: The formability of the die was moderately established in the analysis stage and the S/B was reviewed without consideration of the real trim tool conditions, such as locating and elastic recovery, based on these results. The NC modeling engineer used CAD to perform compensation modeling, applying a manual process to modify or morph the geometry. Drawshell was also applied only in the field by scanning the OP10 part, without considering it in the simulation. Due to this disparity between the simulation analysis method and the tool shop results, many high-strength steel tools had to be re-worked extensively.
Through the course of this process, a lot of time and effort was invested to achieve perfect formability. As in the actual sheet metal forming process, drawshell was applied by the draw springback simulation result to isolate the trim operation and review springback. Then, compensation was carried out using AutoForm software, including NC data modeling with AutoForm ProcessDesignerforCATIA. These software tools allow for a better transfer of information from forming simulation into CAD and enable a direct application of the required geometry modification. This is normally a tedious process that requires the engineer to make individual decisions about how to actually modify the geometry. The manual nature of this process often leads to inconsistent results. By applying compensation loops directly within the simulation software, a balance can be achieved much faster. Furthermore, this final and stable compensation plan can be used within the CAD environment to make surfacing changes all at once. As a result, a Roof Reinforcement made from 1180 material was completed with just 3 press trials, leading to significant cost savings. After using AutoForm’s springback compensation process, IJS was confident enough to set a target of 3 or less die trials for all future high-strength steel materials (such as 980 or 1180).
Fig 1: Measurements from part scan
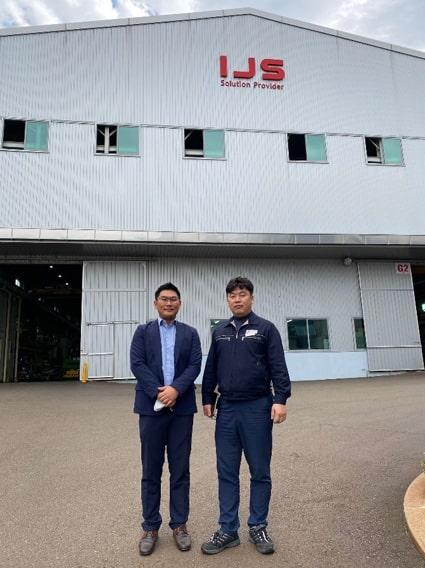
IJS set the goal for 2021 of improving their AutoForm competency to achieve stable results and expand the use of AutoForm to employees involved in die production. In addition, Director Gyeongjun-Jun Cha himself will make efforts to develop new technologies that can be applied to sheet metal forming through the use of AutoForm’s many functionalities.
We thank Gyeongjun Cha, Director of IJS, who greatly contributed to reducing the gap between simulation analysis and tool shop results, fostering an environment of communication and increasing the reliability and usability of AutoForm in IJS. Also, I would like to express my gratitude to Ki-Tae Kim, sales manager of ADE, for his efforts in applying the AutoForm Compensator Process to IJS.
IJS started as Ilji Tech Tooling Factory in 1986 and was established in Gyeongsan as an independent tooling factory in 2014. Currently, the company has more than 100 employees. IJS’s major domestic customers are Hyundai, KIA Motors, and Hyundai Steel, supplying cold dies and hot stamping dies, while major overseas customers include BAIC Motor, KEYLEX Corporation, GAZ Group, and ABTOBA3, supplying sheet metals.