Revisiting Springback Prediction: Advanced Engineering or Correction Loops?
In this blog post find out how Atlas Tool Inc.,one of the US leading stamping die tool shop and low-volume part supplier, has nailed it for springback prediction for a rear cab reinforcement using AutoForm. Yurdaer Demiralp, AutoForm Application Engineer, and Mark Broadworth, tool engineer at Atlas Tool Inc. reveal how you can also expect greater accuracy for springback prediction by utilizing these advanced engineering methods from AutoForm.
Family owned Atlas Tool Inc. is a full service precision manufacturer dedicated to providing customers precision sheet metal fabrication and metal stamping at 29880 Groespringbackeck Hwy, Roseville, MI 48066. The AutoForm simulation software has been used for over 20 years successfully at Atlas Tools to simulate stamping die & tool development processes.
The increasing applications of lightweight sheet materials bring new challenges to numerical modelling of sheet materials forming processes. Especially with the usage of AHSS we see more springback due to its high yield stresses, while aluminum alloys see more because of their lower Young’s modulus.
Fig. 1: Springback magnitude for different materials
The accuracy of results from sheet metal forming simulation strongly depends on the material model characteristics that include the elastic and plastic deformations property which are represented by the hardening curve and the yield surface. In addition, the stress and strain state during the forming process and after tool opening must be simulated accurately in order to achieve reliable springback prediction. It is AutoForm that provides reliable springback prediction with complex geometries and advanced modeling techniques that in the long run saves money spent in tryout.
One all-too-often overlooked approach is the use of kinematic hardening effect of the material instead isotropic hardening. Below we show AutoForm simulations that were conducted to predict springback behavior of a rear cab reinforcement made from Dual-phase, DP600 AHSS sheet material.
Kinematic hardening: what is it and why needed in springback prediction?
In a typical forming process the sheet metal flowing on interface of tooling undergoes complex strain path changes such as tension to compression or vice versa during cyclic loading and unloading.
Fig. 2: The Bauschinger effect or Kinematic hardening.
Isotropic hardening model of a material assumes that the during the unloading (tool opening) Young’s modulus and yield strength remains the same as the loading (see fig.2 – unloading blue line in the stress-strain curve). But, as different research has actually proven, these two parameters do not remain the same but the Young’s modulus decreases just like the yield strength in compression (see fig.2 – unloading red-line): this effect is better known as kinematic hardening or Bauschinger effect.
For a thorough understanding, also the yield surface characteristic of the material changes accordingly.
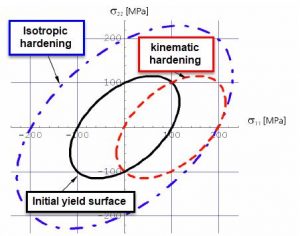
As direct consequence of this effect the springback of the sheet metal is higher than the one predicted using the isometric hardening, and its magnitude increases with the number of loading-unloading cycles the material undergoes during the forming process.
With the help of results coming from different studies, AutoForm developed its own kinematic hardening mathematical model and incorporated it into its early code.
SPRINGBACK prediction with a rear cab reinforcement
In order to compensate tooling based on springback results, dies are often recut several times after initial tryouts. Therefore, an accurate springback prediction with simulation at earlier design stage is extremely desirable to minimize or eliminate additional unexpected recuts of dies.
At Atlas Tool, the stamping process of the rear cab reinforcement, which was the object of this study, consisted of multiple operations, including drawing—with stake beads used to stretch the sheet during the last few millimeters of draw stroke—followed by two trimming operations and a final operation to measure springback was set as well.
Figure 4 shows the sheet after each operation and the final springback measurement map.
Figure 4. Process stages of the rear cab reinforcement within AutoForm.
Setting up the simulation of these and any other operations with the correct process, die conditions, material properties and control parameters to accurately reflect the physical manufacturing process is essential to obtain reliable simulation results. Reliable springback results from a repeatable process help contribute to successful compensation that will reduce or eliminate tool recuts during die tryout.
Fig. 5: Free Springback results predicted by AutoForm
Two different simulations were performed: the first one considering the kinematic hardening effect in the material properties while the second one was not considering it.
The simulations produced springback-prediction results, with draw tools compensated accordingly in order to produce parts compliant with defined and desired dimensional tolerances for the final reinforcement part (Fig. 5). The simulated springback results, employing kinematic hardening modeling, compared closely with actual measurements (Fig. 6), reported Demiralp and Broadworth, noting that the results were significantly better than those based solely on isotropic hardening.
Fig. 6: Measurements of the actual physical panel
As it’s possible to see, comparing the predictions with actual results, the actual measurement matches the predicted panel that considered the kinematic hardening effect in addition to isotropic hardening properties, thus affirming the effectiveness of such simulation.
From AutoForm, we would like to thank Atlas Tools and specifically Mark Broadworth for making this success story possible.
New readers don’t forget to sign up to our blog. We’ll send a once per month update on our latest top post and zero marketing emails.
Further reading:
- Altan et al. “Reducing the number of die recut operations by improving the springback prediction,” Center for Precision Forming, The Ohio State University, Columbus, Ohio, US
- Kubli, et al. “Modeling of reverse loading effects including work hardening stagnation and early re-plastification,” AutoForm Engineering GmbH, Technoparkstrasse 1, 8005 Zurich, Switzerland
- Cao et al. “Experimental and numerical investigation of combined isotropic-kinematic hardening behavior of sheet metals,” International Journal of Plasticity 25 (2009) 942–972
- Yoshida et al. “Material Modeling for Accuracy Improvement of the Springback Prediction of High-strength Steel Sheets,” NIPPON STEEL TECHNICAL REPORT No. 102 JANUARY 2013
- Ming F. et al. “On Springback Prediction in Stamping Of AHSS BIW Components Utilizing Advanced Material Models,” United States Steel Corporation, GDIS.