Introduction
The introduction of forming simulation software has revolutionized the design and execution of complex forming processes, significantly reducing the time and effort required. Tasks that previously demanded extensive trial and error during the try-out phase can now be efficiently simulated virtually. This technological leap has inspired engineers to develop more intricate and efficient part designs. However, refining these designs within the forming software, particularly when addressing issues like springback, can be a lengthy and challenging process. The process of modifying the forming die for compensation is not only iterative but also costly and time-consuming. Therefore, prior to implementing any compensation activities in the forming process, it is crucial to evaluate the impact of the current forming process on the final assembly. This evaluation not only helps in understanding the existing process better but also paves the way for considering optimization in the assembly phase as a viable alternative to part compensation.
In this article, Ramandeep Singh, Technical Account Manager at AutoForm India, presents a compelling case study from the Tier 1 supplier SKH-SMC, India. The study focuses on optimizing the surface in the assembly stage rather than in the forming process, highlighting the importance and effectiveness of this innovative approach.
Product Specifications
The focus of this analysis is on an EV battery pack separator plate, a product developed by the Tier 1 supplier SKH-SMC, India, for an original equipment manufacturer (OEM). This separator plate comprises a two-plate system as illustrated in Fig 1. The system includes a base plate, which is derived directly from the blanking stage, and a structural plate, produced through forming operations.
Originating from India, this project is a collaboration with SKH-SMC Pune, a long-established client of AutoForm. They have consistently used AutoForm’s expertise to design and refine forming processes for various OEMs.
The OEM in this case specializes in the manufacture of electric trucks. These vehicles depend heavily on batteries for their propulsion power, requiring the use of multiple battery packs which are organized into distinct layers, separated by a separator plate. The design of this plate is crucial; it must be flat to avoid contact with the batteries on either side. Additionally, it must adhere to tight tolerances of +/- 0.5 mm to maintain the necessary separation between the battery layers.
Findings from the Forming Simulation of the Structural Plate
The SKH team initially designed and simulated the forming process, anticipating minimal springback in the structural plate due to the numerous embosses incorporated in the final design. However, the first simulation yielded unexpected results, producing a curved part (refer to Fig 2A) that significantly deviated from the intended CAD0 design.
Fig 2A. Side view of structural plate with springback
Fig 2B. Side view of structural plate with springback
The panel exhibited significant springback, with deviations reaching up to 15 mm in some areas (see Fig 2B). This indicated that additional iterations in the forming process were necessary to align the structural plate more closely with the nominal CAD0 part.
In response, the SKH-SMC team undertook compensation activities, coupled with a sensitivity (or robustness) analysis. They realized that achieving the desired form within the specified tolerances could be challenging due to the product and process sensitivity. Consequently, before moving forward, SKH-SMC consulted with our team at AutoForm India to explore potential solutions.
Understanding the intricacies of the forming process and the final requirements of the structural plate, Ramandeep introduced AutoForm’s digital process twin methodology. Using this approach, he performed initial assembly simulations which integrated the existing forming results into AutoForm’s assembly software to assess their impact on the final assembly. He also evaluated whether there were opportunities for improvement during the assembly phase itself.
Exploring Solutions for Assembly Optimization
Users have several options for assembly optimization, including part compensation, shimming, and teaching, among others.
Part compensation involves selecting one or more components of the assembly for compensation based on the assembly results. This process may alter the shape of a part to a non-nominal geometry, but it helps bring the entire assembly within the desired tolerances.
Another method is the combined use of shimming and teaching in the welding fixture. Shimming involves overbending a part or sub-assembly using surface mylars or clamps before applying weld spots. Teaching, on the other hand, entails updating the position of the joining tongs to ensure proper contact with the sheet metal at its new location. Therefore, this approach requires adjustments to both the clamps and the joining tongs. Shimming and teaching are often used together in the optimization of assembled products. For the battery separator plate project, the AutoForm team chose to apply shimming and teaching in their simulations, rather than opting for part compensation in the forming process.
Findings of the Assembly Simulation
The AutoForm team conducted an initial assembly simulation using data from the forming simulation. The results were promising, showing a reduction in surface deviation from 15 mm to 3 mm (refer to Fig 4). Managing a 3 mm discrepancy is significantly easier than correcting 15 mm of springback in the forming process
Fig 4. Surface deviation after the initial assembly simulation
Fig 5. Section view of surface deviation after the initial assembly simulation
Animation 1. Post-assembly drumming effect
Animation 1 provides a valuable visual aid for examining the correlation between the initial assembly processes in both virtual and real environments. It highlights how the center area of the battery separator plate lifts upward due to the deviation noted in the post-assembly process. This effect, mirrored in the virtual simulation, is clearly depicted in the section view (Fig 5).
Further improvements in the assembly stage:
The significant reduction in surface deviation opened the door for further optimization during the assembly stage, rather than the forming stage. The AutoForm team experimented with various methods and validated the results. Shimming and teaching emerged as the most effective techniques, as illustrated in Fig 6, and were subsequently recommended to the customer.
Fig 6. Improved assembly results via shimming and teaching in virtual simulation
Fig 7. CMM observation after first level of improvement via shimming and teaching (try-out results)
The customer was very satisfied with the result. They were able to address the springback issue through assembly adjustments rather than through repeated forming simulations. This approach not only bypassed the need for multiple forming tryouts but also proved to be more cost-effective, as shimming and teaching are less expensive than part compensation.
Advantages of Assembly Optimization
Optimizing through assembly simulation offers several key benefits. Here are some of the most significant advantages:
1. Massive savings in resources:
By optimizing surface deviation during the assembly, engineers can avoid the most resource-intensive phase – optimizing the forming process for each part to ensure seamless assembly. This phase can often span several months and consume considerable manpower and resources to achieve satisfactory results.
2. Easier to handle:
Optimizing the assembly process tends to be simpler and less restrictive compared to forming. This reduces the need for extensive brainstorming and trial runs, making the process more manageable.
3. A Viable Alternative Solution:
In the above case study, if the engineers had not pursued assembly analysis after encountering a 15 mm springback during forming, they would never have recognized the opportunity for optimization at the assembly stage. This highlights assembly optimization as a practical alternative, particularly when forming process analysis does not yield acceptable outcomes.
Conclusion
Assembly analysis has proven to be a game-changer, streamlining the process and enabling a quicker achievement of the desired part assembly. Approaches like shimming and teaching are notably more manageable than undertaking compensation in the forming software. By focusing on adjustments during assembly rather than in the forming stage, we can efficiently achieve the final part specifications.
The only limitation lies in the accuracy of the software, its ability to model various assembly processes, and the expertise of the user. These factors are crucial in determining the success of assembly optimization.
From Kishore Patnaik:
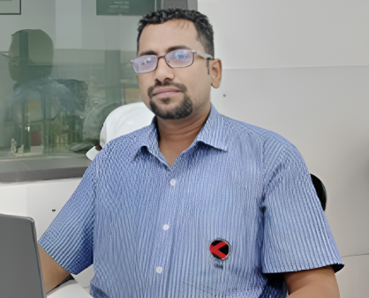
It was an exciting journey to experience the correlation between the virtual and actual realms at every stage of product development. Working in collaboration with the toolmaker and weld integrator, we shared the common goal of achieving a flawless end assembly of the battery pack separator plate, free from unexpected surface deviations.
I was thrilled to observe consistent results at every stage— starting from AutoForm forming simulation to assembly simulation, and finally implementing shimming and teaching to perfect the product.
Being part of this exciting journey has been a source of immense joy and satisfaction!
With thanks to Mayank Gupta, Ramandeep Singh, Shiju KT, Girish Sethi, Raghuram Shenoy, Ravikumar, Shekhar kadam, and Hanumant Amte.