Case Study Opens Sustainable Growth and Business Evolution
In this blog post Ms. Natsumi Goda from the Stamping Engineering Department at Nissan Motor Company (hereafter Nissan), reveals a never before seen evaluation project performed for a hood-outer part. This was one of the first ever testing of the TriboForm Software in Japan! Nissan is an AutoForm customer and wanted to examine how the TriboForm Software might highlight surface defects that had not previously been detected in their sheet metal stamping simulations. See the results below.
The emergence of new technologies, such as electric vehicles and autonomous driving, means the global automotive market has become increasingly competitive, with companies continuously looking to gain an innovative edge in this fast-changing environment. To adapt to this environment, Nissan is actively engaged in a revolutionary transformation process across all areas of its business, from car design and development through to production, sales and service.
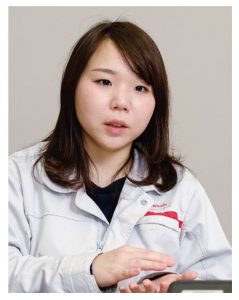
Nissan has formulated a six-year midterm plan, named “Nissan M.O.V.E. to 2022,” covering the years 2017 to 2022, as it looks to accelerate its efforts for long-term sustainable growth and development of the business
At the same time, Nissan offers new technologies and products through its vision of “Nissan intelligent mobility” leveraging technological advances such as electric vehicles, autonomous driving, connected cars, and accelerating the development of new mobility services through new technologies and businesses.
Detecting surface defects by integrating TriboForm into stamping simulations
The core objective of the company’s business plans is to produce attractive products for its customers. Worldwide, Nissan offers a range of highly original and innovative products, including models such as DAYZ, SERENA, NOTE, LEAF, X-TRAIL, and JUKE. In recent years, customers have particularly been looking for cars that incorporate a full range of design features as well as reduced weight. As design technology evolves, the increased complexity of stamping tools and parts introduce a new challenge. At the same time, manufacturers need to shorten their development lead-times in order to respond promptly to the demands of the market. Ms. Natsumi Goda from the Stamping Engineering Department in the Vehicle Production Engineering and Development Division explains, “To speed up development, it’s essential to shorten the required time due to more challenging tool designs and also simulation processes.”
To respond quickly to such market demands, Nissan uses the AutoForm software which has a significantly shorter analysis and simulation time compared to competitor products.
However, Nissan had found that some surface defect issues were not being detected by the company’s previous simulation process and inspection methods and only came to light after stamping. To solve this problem, Nissan used AutoForm to evaluate the panel’s surface quality during and after the forming process. When surface defects occur, this often means that the design or forming process has to be adjusted which can have a major impact on the lead time. As a result Nissan decided to become the first Japanese OEM to test the TriboForm software, a tool for simulating friction and lubrication conditions in stamping simulations. The company decided to carry out an evaluation project with the intention to integrate TriboForm into the simulation process if the project was successful.
Sheet metals used in car body parts have specific surface properties. The material type used and the surface roughness affects tribology and friction in the forming process. The TriboForm software allows users to quickly simulate the effects of tool surface coatings, lubrication type, material surface characteristics or new tool and sheet materials on friction and ultimately on product quality; it is also easy to use. The user simply defines the material type and surface roughness of the tool and sheet material and specifies the type and amount of lubricant that is used in the forming process. After integration of the more realistic friction and lubrication conditions in the stamping simulations, the software can more accurately predict panel surface defects that will occur during forming.
Figure 1. Comparing the surface defects in the real panel (top image) with the simulation results (bottom image) shows that some surface defects were not detected when using a constant coefficient of friction in the stamping simulations (white arrow showing the missing surface defect in the simulation, while present in the real panel).
According to Ms. Goda, “AutoForm simulations can usually be run with a constant coefficient of friction. However, we found that some panel surfaces were defective because of surface defects in production. With TriboForm you can use a variable friction coefficient in the stamping simulations which varies by location and in time, rather than a constant value. So, we decided to assess whether a more accurate friction description would result in the detection of surface defects.”
Accuracy rate up 20% using TriboForm; Detection errors cut by 10%; Lead time reduction
The assessment was carried out by Nissan in 2017 over a period of six months. The evaluation project focused on an aluminum hood-outer part. This time the stamping simulation was run on a stamping tool where surface defects had occurred on the part (as shown in Figure 1) to see whether the software could predict all the defects.
In fact, the AutoForm simulation including the TriboForm friction model detected a panel defect which had not been picked up by the conventional simulation method using a constant coefficient of friction, as shown in Figure 2. Successful detection of defects that would have been overlooked previously has increased the Nissan’s simulation accuracy by 20% and also reduced the lead time of such panels. “Furthermore, some false surface defects were detected using the conventional simulation method which have declined by 10% using AutoForm with TriboForm.” says Ms. Goda.
Figure 2. The surface defects found in the real panel (top image) were detected in stamping simulations when using TriboForm friction models (see the right images, indicating TriboForm). Some defects could not be detected when using a constant friction coefficient (see the left images, indicating the conventional simulation method).
Using the TriboForm friction models in AutoForm, Nissan was able to predict surface defects that were not found using a constant friction coefficient, as shown in Figure 2. “You have to make sure that the input parameters of any simulation are consistent with the real stamping process, and we found that the combination of AutoForm and TriboForm showed excellent results” adds Ms. Goda. “In the future, we would like to investigate how the tribology-related input parameters can be obtained efficiently corresponded to the end process when using AutoForm.”
Currently Nissan uses the default TriboForm friction models which is provided with the TriboForm software. However, the default TriboForm library deviated to some extent from the exact material grades and lubrication types of Nissan’s parts. Currently, customized libraries based on Nissan’s specification are being generated to continue and increase the use of the TriboForm software at Nissan. Ms. Goda goes on, “we expect to further improve the simulation accuracy using Nissan’s customized libraries.” Evaluating surface quality for different analysis ranges and material types with accumulated test data.
After completing the evaluation project, Nissan officially started to use TriboForm. TriboForm is now integrated in the stamping simulations by the Stamping Engineering Department. In the future, in addition to simulating the hood-outer part described in this study, Nissan plans to expand the scope of its analysis to doors and fenders and to build a database of test results by running simulations of different material types such as aluminum and mild steel grades.
“Our impression of TriboForm is that it’s really easy to use and to understand. All you need to do is to specify the material and lubricant that you’re using. In fact, we encourage our engineers to find new applications and ways of using it.”
TriboForm simulates friction conditions to help users shorten the lead time required for development and to aid cost reduction. Using it has enabled Nissan to improve accuracy levels in its simulations.
New readers don’t forget to sign up to our blog! We’ll never send you any marketing emails. You’ll get a once per month update on our latest top post!