AutoForm Senior Process Consultant Offers Best Practices
At AutoForm we often realize that as soon as we talk about HSS and AHSS the discussion quickly goes to springback related issues. In fact, springback immediately becomes the center of attention. Several questions are asked: such as what new strategies are available to deal with a certain problem? And, why does our standing know-how gained from previous projects not work as planned when applied to parts from this material? Who and what can then help to overcome these obstacles?
In addition are times when customers have even asked “Why is springback suddenly an issue, when it was not any issue at all with other materials?” Yet, it should not be a mystery that when moving product designs that previously worked with materials of 200MPa as its yield strength to those of 600MPa that springback potential has tripled in reality, making the production of those parts far more difficult.
Predicting springback is a matter of taking the forming stress in your deformed material and dividing it by its elastic modulus. If the math is that simple, then why is there all this fuss about springback prediction being difficult for these higher strength materials?
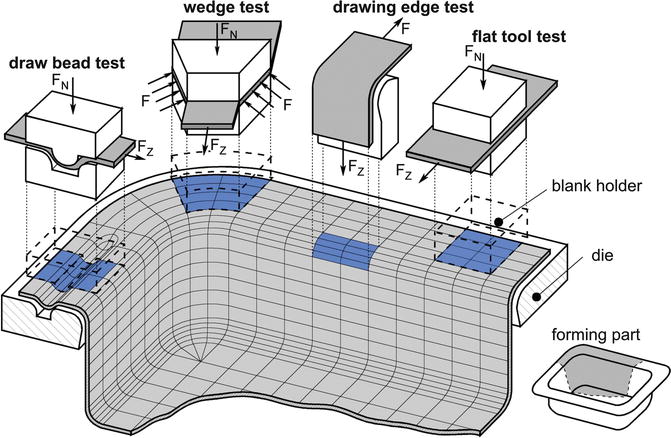
In reality we are not producing anything like simple test samples, being stretched in uniaxial directions. Real parts will have different strains distributed throughout the geometries. And strain distributions can vary from part to part during normal production conditions. When any aspect of the forming process changes we too could see differences in the distribution of in-tool stretching, which changes the distribution of springback effects through the part itself, and possibly providing very different effects on the final part shape.
How do you plan for and accommodate the possibility of varying springback in your parts during production? What measures do you take to correct springback to assure robust production results for your customers?
Along with having to deal with the springback risks of AHSS let’s not forget the risk of cracks during forming. In in engineering automotive parts we always have to reduce the risk of cracks by paying special attention to having a homogeneous geometry. Now it becomes a game of avoiding steep frame angles (in the working direction). As well, the goal of process design is getting as much stretch as possible over the entire part. The consequence of facing higher strains in the component means that the springback strategy must, consequently, be even more robust.
But, a springback compensation strategy is only robust if it’s achievable and repeatable: turning out thousands of manufactured parts.
Nailing Springback in its Place
Springback is determined by the material properties. It is also important to be aware of the fact that each additional forming step introduces new stresses into the component that reduce its ruggedness and at the same time increase springback. So, in engineering it’s important to plan as few forming steps as possible, both during part design and during method plan development.
The three golden rules for successful compensation also apply to high-strength steels:
- Understand springback
Ask yourself, by which boundary conditions is springback mainly influenced?
For example: operations and operation contents.
- Reduce springback and ensure process stability (robustness)
Ask yourself if it’s possible to reduce the springback by changing either the geometry or process parameters?
- The method plan (avoid restrike operations)
- Construction, blank holder etc.
- The part geometry.
- The tool geometry.
- The process.
- Compensate for springback
Ask, which “compensation strategy” is the most effective and efficient?
Let’s not forget to pay attention to the forming forces. These are significantly higher with high-strength steels. With the higher forces – the wearing in the tool also increases and therefore also materials and coatings must have a higher quality. It is also important to ensure that the press has sufficient strength that it may completely stamp out the component. If this is not sufficient, for example, any comparisons between simulation and reality are extremely difficult and virtual compensation becomes impossible.
Further, the cutting forces increase significantly to handle the task. These increase until the part to be trimmed yields. The entire force is released in seconds and is transformed into kinetic energy. Therefore, in trimming operations, it is important to evenly distribute the cutting forces and to reduce them by dimension such as roof-shaped blade edges, sequential cutting or applying cutting-shock-dampening.
The Overlooked Rule of Nailing Compensation in Simulation
Lastly, AutoForm recommends emphasizing the following concepts:
Simulate only what is technically feasible.
Apply to the technical what was simulated.
In order to achieve the result obtained in simulation – it is necessary (especially when dealing with high-strength steels), that the same parameters used in the simulation are going to be the ones used in reality. It is important that input parameters such as current material types, blank size and position, blankholder forces, tribology, tool kinematics etc. are also those seen in reality. Our tests have shown that some input parameters can be so sensitive that any small changes can have massive consequences in simulation results. Experience has shown accuracy is not a problem of the software, but it becomes an issue when there are differences between any processes carried out in simulation and in practice. These differences can only be avoided by ensuring intensive communication occurs between tool tryout teams and engineering teams to verify that everything matches.
You may also want to take a look at our AutoForm’s Springback Compensation Best Practices article which outlines the ideal simulation set up.
New readers don’t forget to sign up to our blog! We’ll never send you any marketing emails. You’ll get a once per month update on our latest top post!
* Cover image courtesy of Weba.