In this interview Bart Carleer, Corporate Technical Director and member of AutoForm’s Board of Directors, outlines AutoForm’s future, its milestone successes and his views on how AutoForm can still better serve the sheet metal forming community.
We put the following questions to Bart:
What are the biggest obstacles AutoForm customers face in the stamping process chain today?
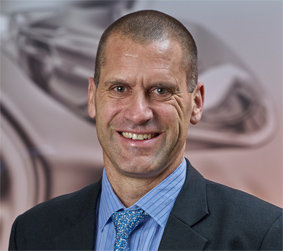
I see two main potentials for improvement in the field: speeding up the engineering process chain to better meet deadlines and sharing valuable engineering data with other teams in the value stream to reduce double work and improve quality.
Naturally, tool suppliers and part manufacturers face ambitious deadlines. ‘We are up to our neck trying to meet deadlines’ is their rebuttal to training offers. However, spending time learning AutoForm and expanding their simulation and modelling know-how is a worthwhile investment. Learning to better master our solutions means that the execution of many engineering and planning tasks will be shortened, a lot of time will be won back for the company while at the same time the quality of simulation predictions is increased.
Faced with tight deadlines, it is very important that the digital engineering process is started as early as possible – starting early with feasibility analyses saves lots of time reducing the number of iteration loops in process and tool engineering later.
Since many questions regarding tool and process design can – in fact – be answered quite early in the process chain, the propagation of results generated during feasibility analyses is very useful to inform those who take over the workflow later on. AutoForm supports the sheet metal engineering process in this regard with our one-file concept which makes it very easy to exchange process data with others. We do not only deliver software tools – we also deliver the whole methodology and complete workflow support. AutoForm has a proven track record of shortening work phases towards reaching the final goal.
The other major process improvement potential regards internal communications and data propagation. This is one of the major factors to successfully reducing turn-around times and delays. The transition of data – not only to the tryout teams, but throughout the entire process chain – can resolve bottlenecks and reduce extra work costing time and money.
Today, it is easily possible to support and empower the tryout teams with meaningful engineering and simulation data. Feasibility data and process concept data can be made available, for example, to CAD die design teams. Sometimes these tasks are performed in entirely different departments. Information loss or disconnects in the information flow can lead to a variety of issues:
Data often needs to be re-created or re-engineered – upstream analysis for final validation and compensation can identify discrepancies generating new and unnecessary, time-consuming iteration loops. After the tool design is completed data is sent to tryout.
Here, a close cooperation of engineering with try-out teams is essential. We have observed that – in some cases – the involved teams are not interacting in a meaningful way. It’s something I call the ‘not invented here syndrome’ whereby the work of others, created in other departments, is simply not being used although it is available. In these cases, massive amounts of information are being lost and the entire process is invented again from scratch leading to delays, information discrepancies and unnecessary iteration loops.
This – in my mind – is the biggest hurdle to success. Die design teams might, for example, not take into consideration all of the data which has been provided by their engineering or feasibility departments. In such cases the process validated with AutoForm during the engineering process is not executed but is rather challenged by downstream teams who each have their own way of working. A seamless workflow where all available engineering data is freely shared down- and upstream bears a huge savings potential for many of our customers.
What are the most under-utilized innovations that could be implemented right away?
It’s still the stochastic analysis and prediction capabilities of our product AutoForm-Sigmaplus. The song of many process engineers is ‘we are too busy and can’t find the time to use Sigma.’ But let’s take a close look at this argument. I am convinced that users of AutoForm-Sigmaplus will be more successful meeting their deadlines. It is the old song ‘I cannot stop to sharpen my axe because I have to cut down all these trees.’ AutoForm-Sigmaplus is known to get results quickly, especially its SPI (Systematic Process Improvement) application speeding up the engineering process. For most of our users who have already undergone the training it’s taking the next step applying it in their daily tasks. Many of our customers who have taken this step have found out how Sigma improves their work and speeds things up avoiding unnecessary loops. Many published examples have shown that AutoForm-Sigmaplus simulations are done to such a level that they will indeed avoid correction loops in real tool tryout. In Japan customers have even achieved a ‘One Loop Tryout’ for the creation of 70% of their tools for the stamping of parts.
What do users experience after training? How independent are they?
Seeing that AutoForm is easy to use and intuitive, it all comes down to taking care of the details for achieving final validation analyses. A lot of details need to be kept in mind setting up real sheet metal production processes – and the same is true for the simulation set-up. As always, the devil is in the details, and this awareness is gained during increased use of our software. During initial training you learn how to handle the software. After that new users have to gain experience through use and setting up simulations in a meaningful way – representing exactly how the company works in their toolshop or tryout shop.
This is a step we support but, of course, this goes beyond a software base training. Rather, this is done through support, working together. We even can go on-site to help set up the software, so it’s working in such a way that simulation reflects precisely the reality of their own tool shop or their particular customer. Users need support after training, some more, some less, since these little details are customer-specific, according to their particular way of operating. We offer support during this integration after training. So it’s not just a matter of diving into the software right after basic training. The implementation is the key and AutoForm Support serves as a consultation service for engineering improvement as much as a software provider.
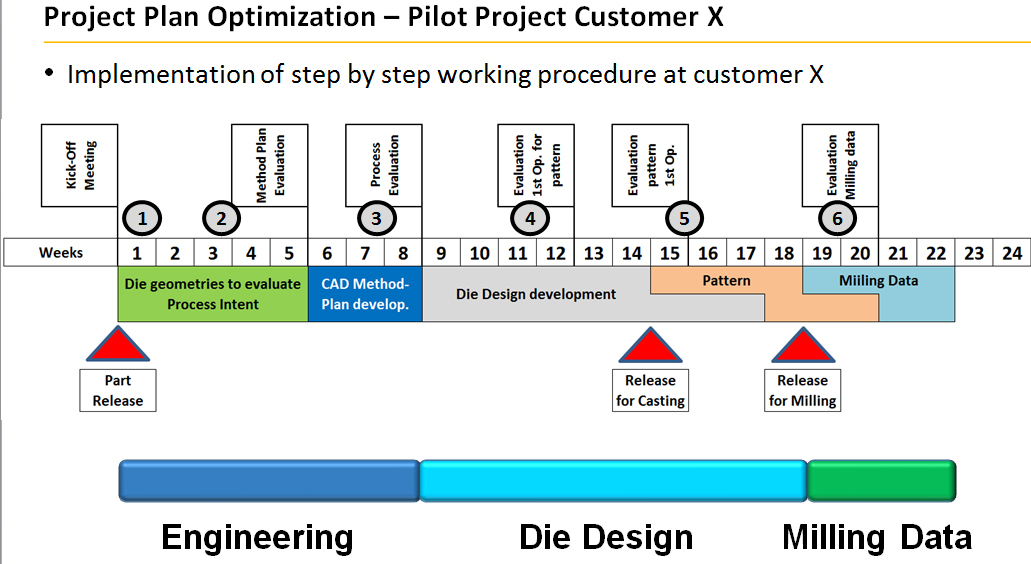
You’ve mentioned savings generated using AutoForm solutions. How exactly can customers realize these time and money savings?
First we must examine the main savings, which are won in tryout. On average the tryout phase costs 20-30% of a tool’s total cost. In the past it was even more. AutoForm has already achieved a major win by reducing the number of tryout loops through process simulation and validation. Ten years ago tryout meant time spent in feasibility issues, dealing with splits and wrinkles. Nowadays those 20-30% can, in fact, easily be halved again by performing springback compensation during engineering. Thus savings can be realized engineering better tools. On the other hand, savings that are not clearly visible in the engineering phase involve the engineering of robust processes. Our aim is to help our customers achieve zero defect production. To reach that goal, reliable and robust stamping processes need to be engineered and validated prior to production start. Huge cost savings are in reach using this technology, avoiding the creation of scrap material. Furthermore if you have to produce 100,000 parts you also have more reliable production planning data.
By including the AutoForm Planning and Bidding Solution (PBS) you’ll have far fewer surprises downstream. PBS not only predicts costs, but it also lets you predict what is going to happen in terms of piece cost in far better detail at a very early stage in the engineering process chain. Of course, our customers work in a very competitive field and are constantly challenged to improve every aspect of production that will save them money and increase speed. This is all distilled into their models for planning as well, which need to be constantly monitored in order to be up to date. By increasing the use of this software your predictive cost-planning and reality come ever closer together. PBS means your predictability increases in terms of engineering time etc. Once plugged into the ERP system of the customer it becomes extremely powerful.
What then are some of the tangible milestones AutoForm has achieved in terms of offering new tools never seen before?
Starting from the beginning, one clear milestone occurred 20 years ago when our solver came onto the scene. At that time only deep drawing simulations were available, and our solution provided the answer in just half an hour. That was revolutionary at the time. AutoForm as a brand became well-known. We effectively brought simulation out of R&D and into the engineering teams. Shortly after that in 2000 we introduced AutoForm-DieDesignerplus allowing users to generate concept die surfaces. You could design a drawing tool in minutes to a half-hour whereas in CAD you needed a full day. The third innovation was the full integration of die face creation with simulation pre- and postprocessing capabilities in one easy-to-use user interface. Now users could rapidly perform analysis loops, simulating and modifying their die designs. These are major innovations by AutoForm that have really revolutionized sheet metal engineering.
AutoForm was also the first to advance this technology to include automatic trim line optimization. Then we started development of AutoForm-Sigma, where instead of focusing on a specific process point we made it possible to examine a real process window. This created our famous ‘robustness analysis,’ which has given part manufacturers repeatable results within a process window that would be able to handle the inevitable variation of the input parameters (e.g. material quality). Of course SPI was first done by us, which was a real innovation to optimize the forming processes and to provide meaningful data to optimize production of sheet metal parts.

What we also did was to enhance our process planning tools for defining a process plan and doing cost calculation in a more illustrative way. Now the process plan is better visualized and can be better built up as a reference to understand not only the drawing but also the entire process. AutoForm’s introduction of the process plan creation may also be seen as an important milestone to the evolution of simulation. Nowadays it is the standard for defining all process simulations. All operations, including how a part falls out of the press, are defined and accessible to all planning, engineering and validation activities.
What’s the main challenge in body engineering today, how does AutoForm contribute to mastering this challenge and what about the future of AutoForm?
(Bart laughs). At this moment in time, there is hardly any simulation of deformable bodies available to body engineers. The current state-of-the-art is forming sheets into parts. However, currently, we are working on expanding the analysis capabilities to the forming of individual units into assemblies. Today body engineering simulation capabilities are looking at kinematics only, examining how you can fit and bring the parts together, more or less as rigid bodies – examining the important question of ‘does it kinematically work?’
However, we are now at the frontier of something new – we are now introducing deformable bodies into body engineering, taking into account the entire forming pre-history and deformable parts into body engineering. In the near future we will talk about geometrical tolerances of assemblies which is a new dimension rather than talking about kinematics. This will have significant consequences for the entire body engineering process and open up totally new savings potentials. Until now, geometrical tolerances have all been fixed in the body shop. Now we are headed in the direction ‘No, you can fix it already during the engineering process, by properly simulating the hemming and assembly process.’ The assembly result incl. compliance with geometric tolerance targets will be predicted in advance so you don’t end up confronted with tolerance issues in the body-shop itself. In the past, we have reduced time in tryout. In the future we’ll also reduce time in assembly.
This is a natural development in the evolution of AutoForm. We do – after all –focus on forming and we expect to revolutionize the body-shop next if our customers indeed start performing engineering simulations on deformable body parts and assemblies instead of only looking into kinematics. This is the next phase for AutoForm along with looking at hemming ties into assembly. We’ll no longer deal with single parts but examine the entirety in simulation starting 2019.
Thank you Bart for this insightful interview!
New readers; sign up to our blog to stay informed. We’ll send you just one email per month featuring the top four latest posts. Want to share your own article on our blog? Contact us to start contributing.