Inside the Tryout App from Tryout Solutions
FormingWorld.com welcomes another guest post, this time coming from Thomas Kleiner, Geschäftsführer at Tryout Solutions. He joins us to share with our community more information about their latest app for improving tool and part delivery to OEM customers.
As a service provider specializing in the field of stamping and forming technology we observed a growing need to improve the tryout process worldwide. Our customers needed to track the quality of their tools, during both development and ongoing tool production. This is the story of how our ‘Tryout App’ came to be and how missing information caused all too many headaches.
Although the tool removal process is very important for the documentation of the tool quality and thus for the subsequent incorporation on the production press, this step is subject to a lack of time seeing that tryout must be done quickly and reliably. If defects still exists they must be communicated by the tool manufacturer, and let’s not forget the state of the tools needs to be checked and documented before shipping. A growing need arose for detailing all this information.
Today’s press shops work under tight deadlines and therefore cannot dedicate enough time before moving on to the next tool. For this reason, it becomes enormously important that the tools are already delivered with good quality in the production press shop.
Everyone seemed to be doing hour-long follow ups of their reports, even carried out in hotels after a day spent in consulting, or done tediously during overtime hours at work. The subject and limitations of the checklist as well as the existence of the current design guidelines presented their own issues. This is not to mention the fact that often we see reports that STILL have to be manually filled out in paper form, only later needing to then be transferred to Excel or another system. What a mess!
The call was clear and this led us to develop a Tryout App for the entire process. We listened to customer requirements and realized that such an app must be able to provide a specific checklist according to each customer’s standards and modelled to apply to any type of tool.
So, what’s inside our app?
Employees can work through stored lists, step by step, and need only click an “okay”, “not okay” – “not relevant” or “evaluation pending” etc. button for each item.
In addition, you can write a note at each point and attach a picture or video to your comment. This includes relevant data such as tracking who added which comments and pictures, of course when etc. The contact person and such data can be retrieved at any time.
Once the acceptance has been completed, another check can be run to see if all points have been processed. The report is then sent by merely pressing a button to the pre-stored contact and thus arrives to the customer, project manager or supplier before the “tool – buyer” has time to get home.
Fig. 1: Inside Tracking for the Tryout Solutions App
Next the quality and the compliance of the guidelines are simply tested and documented to the customer and in reverse data may be communicated back to the tool supplier.
Following this, it’s very easy to roll out new releases. Once the checklist has been uploaded, it is immediately available to every employee worldwide on every tablet. What’s more, you will still be able to call up any relevant and current design guidelines at every point.
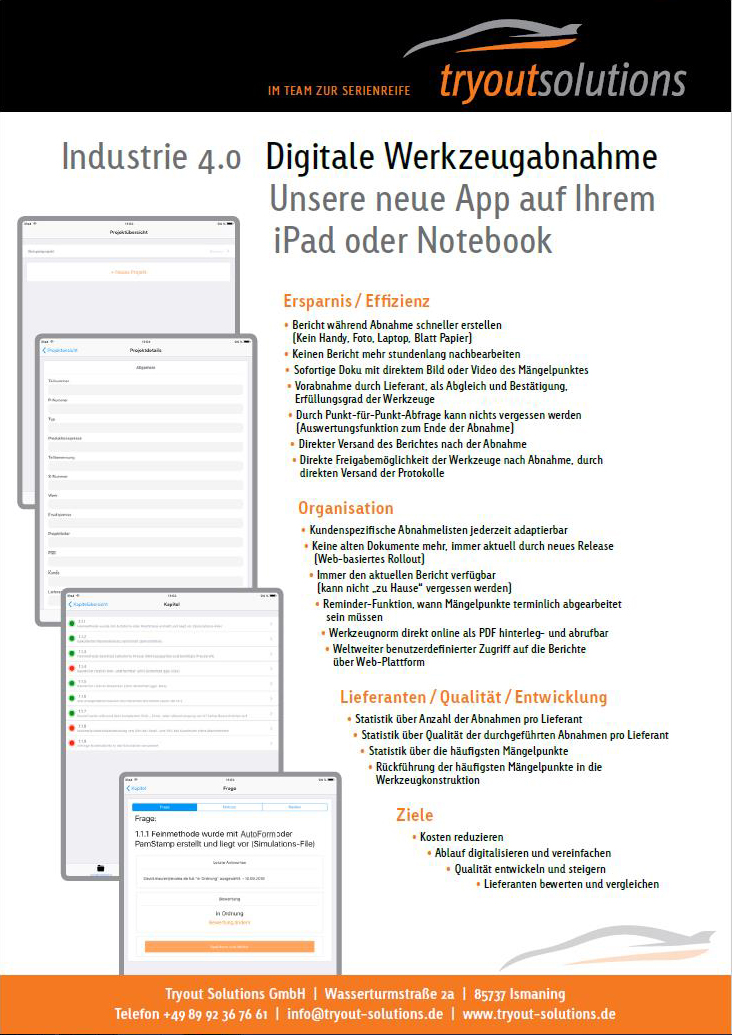
Here is where it gets interesting. What about statistics and bottlenecks? We advanced things further developing a web interface. Now statistical evaluation functions are available, such as the average degree of fulfillment, of all acceptances, or the filtering to the most frequent deficiency point.
Ultimately, we have put a lot of focus on an easy-to-use interface, so no training is needed for some, for others it’s a breeze to quickly learn. This is the easy-to-use digital tool for your daily work.
Contact details to find out more:
Mr. Thomas Kleiner,
Tryout Solutions GmbH,
Wasserturmstraße 2a,
85737 Ismaning
info@tryout-solutions.de
*Note: See our Guest Post Disclaimer here.